Hourly workers play a crucial role in on-site specialist tasks like equipment maintenance and machine operation and essential services like security and surveillance within manufacturing. However, according to Gartner's predictions, a seismic shift is underway. By next year, 50% of factory work will transition to remote operations. This signals the advent of virtual teams becoming a tangible reality in the industrial sector.
Remote factory operations involve using advanced technology like IoT and specialized tools like 3D printers to manage and monitor manufacturing processes from a distance. The use of cutting-edge technology facilitates real-time remote monitoring, ensuring seamless oversight of operations. This approach empowers industries to streamline workflows, enhance efficiency, and adapt to the evolving demands of the modern workplace.
As the manufacturing sector embraces this shift, remote monitoring becomes paramount. This involves using innovative tools and technology to supervise operations. It helps in agile decision-making and proactive management. The integration of these tools helps optimize performance and aligns with the industry's trajectory toward a more flexible and technologically advanced future.
The Importance of Remote Operations in Manufacturing
Remote factory operations in manufacturing have become significantly crucial due to the COVID-19 pandemic, which led to the need for social distancing and remote work. However, the adoption of remote operations has also been driven by the need for efficiency, cost reduction, safety improvements, and addressing skills gaps. Here are some key points highlighting the importance of remote operations in manufacturing:
Driving Efficiency
Remote factory operations drive efficiency by enabling real-time monitoring and data-driven decision-making. A Science Direct study confirms a positive relationship between remote operations and efficiency. Through the use of advanced technology and specialized tools, manufacturers can remotely oversee production processes, identify bottlenecks, and optimize workflows swiftly. This approach helps minimize downtime, enhances resource utilization, and streamlines operations for maximum output.
Cost Reduction
Remote factory operations leverage cost-effective tools such as IoT sensors, automated guided vehicles (AGVs), and cloud computing to drive substantial cost reduction. These technologies enable real-time monitoring, predictive maintenance, and efficient resource management. For instance, IoT sensors provide data for predictive maintenance, minimizing downtime and repair costs. AGVs streamline material handling, reducing labor expenses. Cloud computing centralizes data, enhancing collaboration and minimizing infrastructure costs. The strategic use of these tools aligns with cost reduction goals, making remote operations financially efficient.
Boosting Safety
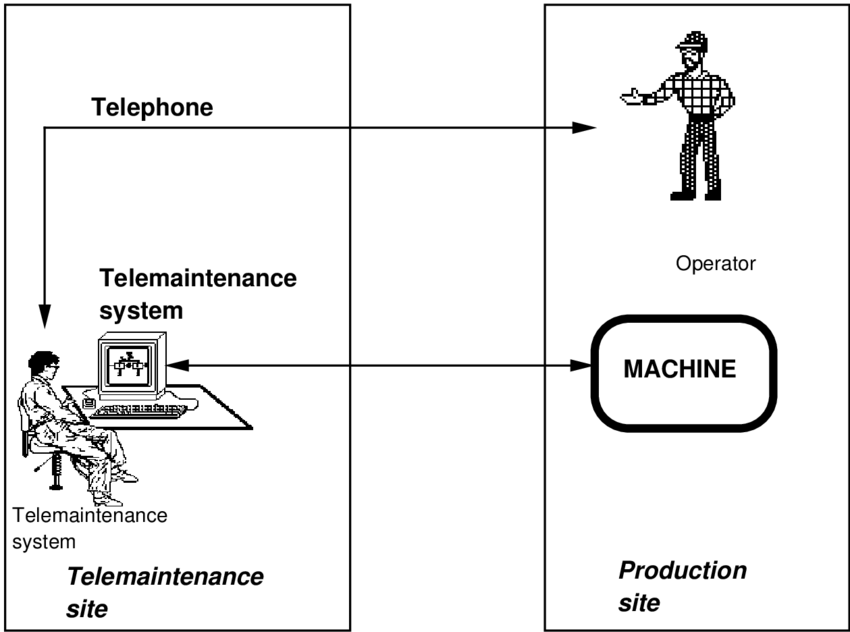
Remote factory operations help enhance safety through the implementation of advanced tools such as drones for surveillance, telemaintenance systems, and collaborative robotics (Cobots). Drones provide real-time monitoring, reducing the need for workers in potentially hazardous areas. Telemaintenance systems enable remote diagnosis, minimizing the exposure of on-site personnel to potential risks. Collaborative robotics ensures the execution of tasks with precision, mitigating safety concerns. The strategic use of these tools fosters a safer working environment by minimizing direct human involvement in high-risk situations.
Alleviating Skills Gaps
Remote factory operations play a crucial role in alleviating skills gaps by employing tools such as augmented reality (AR) maintenance apps and Cobots. AR maintenance apps provide remote technicians with virtual guidance, reducing the need for specialized on-site expertise. Collaborative robotics allows workers to collaborate with machines, bridging skill gaps and enabling less-skilled personnel to contribute effectively to manufacturing processes. These tools empower a diverse workforce, addressing skill shortages and promoting a more inclusive and adaptable manufacturing environment.
Adapting to Changing Circumstances
Remote factory management is very valuable in helping operators adapt to changing circumstances, such as the challenges posed by COVID-19. By leveraging tools like remote monitoring software, collaborative robotics, and virtual collaboration platforms, manufacturers can easily adjust workflows to accommodate remote work setups. These technologies enable continued production oversight, maintenance, and collaboration, ensuring operational continuity in the face of disruptions. Remote operations thus provide a resilient framework that facilitates swift adaptation to unforeseen circumstances, maintaining productivity in dynamic and challenging environments.
Types of Factory Workers That Can Operate Remotely
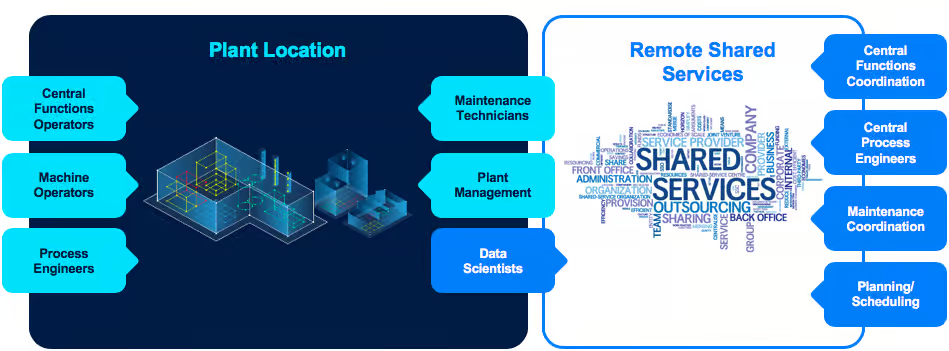
Not all factory workers can operate remotely as some jobs require physical interaction with machinery on the factory floor. However, below are some that can comfortably be done remotely:
Data Scientists
Data scientists analyze complex data sets to get good knowledge that they will then use to optimize processes like predictive maintenance and workflow efficiency. Data scientists can use secure virtual private networks (VPNs) or cloud-based platforms like AWS, Azure, Google Cloud, etc., to access the factory's data infrastructure when operating remotely. They connect with the factory's systems through encrypted channels, enabling real-time analysis and monitoring of production data.
This setup often involves collaboration with on-site technicians to ensure easy integration of data sources. By leveraging advanced analytics tools like Tableau and Apache Spark and communication platforms like Slack and Microsoft Teams, data scientists remotely contribute to process optimization, predictive maintenance, and overall efficiency in manufacturing operations while maintaining data security protocols.
Central Functions Coordinators
Central functions coordinators oversee critical functions such as logistics, supply chain management, and resource allocation within a manufacturing setting. They use secure VPNs or cloud-based platforms to access the factory's centralized data systems remotely. These coordinators actively organize and optimize various aspects of manufacturing processes through encrypted connections.
Virtual meetings and collaboration platforms enhance communication with on-site teams, allowing for real-time updates and strategic decision-making. This remote setup ensures seamless coordination of central functions, promoting efficiency, and adaptability in manufacturing operations while maintaining data security and accessibility.
Central Process Engineers
Central process engineers are professionals who monitor and optimize manufacturing processes within a centralized framework. They also remotely access the factory's data infrastructure through secure VPNs or cloud-based platforms. These engineers actively analyze real-time data, identify process bottlenecks, and implement optimization strategies.
They collaborate with on-site teams using video conferencing and communication tools like Zoom to coordinate process adjustments and enhancements. This remote setup ensures continuous process improvement, allowing central process engineers to contribute to operational efficiency and adaptability while maintaining connectivity with on-site personnel and ensuring the security of critical manufacturing data.
Maintenance Coordinators
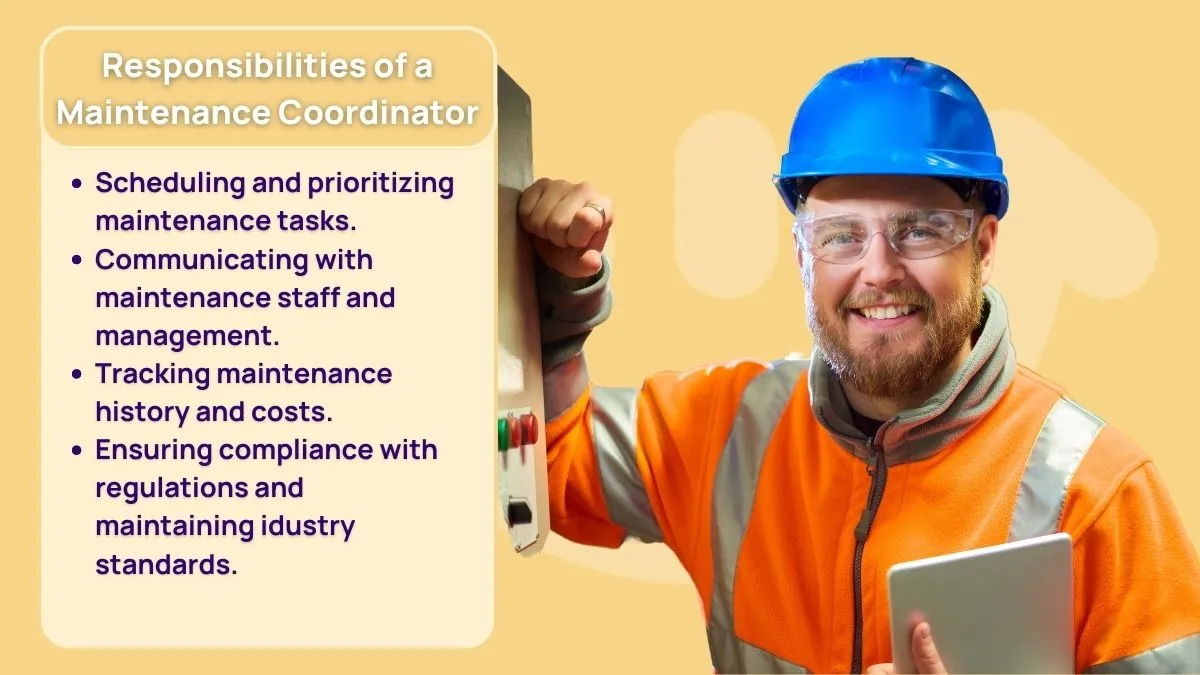
Maintenance coordinators are professionals responsible for overseeing and coordinating maintenance activities within a manufacturing facility. Utilizing video conferencing and communication tools, they actively collaborate with on-site maintenance teams to schedule, monitor, and troubleshoot equipment.
This remote setup allows maintenance coordinators to conduct virtual inspections, provide guidance for repairs, and ensure timely maintenance without the need for a physical presence. By connecting seamlessly with on-site personnel, they contribute to efficient maintenance processes while maintaining data security protocols.
Planners/Schedulers
Planners/schedulers are professionals tasked with coordinating and optimizing production schedules, resource allocation, and workflow timelines within a manufacturing setting. They also remotely access the factory's scheduling and production data through secure VPNs or cloud-based platforms. They actively engage with on-site teams to plan production cycles, allocate resources efficiently, and adjust schedules as needed.
This remote setup helps Planners/Schedulers to adapt to changing circumstances. It ensures they have easy communication and coordination with on-site personnel while maintaining the security of production data and contributing to the overall efficiency of manufacturing processes.
Remote Monitoring of Factory Employees
Monitoring employees remotely helps effectively manage factory workers, and it has many benefits. By implementing remote monitoring systems like IoT sensors and employee monitoring softwares (Teramind, ActivTrak, etc.), employers can actively oversee and track the activities of their workforce, ensuring that tasks are executed efficiently and in accordance with established protocols.
This extends to performance monitoring, where key performance indicators are tracked and analyzed to gauge individual and collective productivity. The benefits of this approach are multifold. Employers can identify areas for improvement, provide targeted feedback, and offer timely support to enhance overall performance.
Remote monitoring promotes accountability among workers and facilitates a data-driven approach to workforce management. It enables employers to recognize high-performing individuals, address potential challenges promptly, and optimize workflows for maximum efficiency. Moreover, the real-time nature of remote monitoring ensures that interventions can be timely and targeted, contributing to a dynamic and adaptive work environment where workers are empowered to excel and the overall productivity of the factory is maximized.
Challenges and Risks in Implementing Remote Factory Operations
Implementing remote factory operations comes with several challenges and risks that organizations must navigate. These include:
- Latency and communication challenges. Distance and latency can make it difficult for operators to respond quickly to issues or communicate effectively with on-site personnel.
- Cybersecurity risks. Remote operations increase the risk of cyberattacks, making it crucial for manufacturers to implement robust cybersecurity measures.
- Difficulties with training and skill development. Ensuring that workers have the necessary expertise to operate remotely is crucial for the successful implementation of remote operations. Inadequate training can lead to errors and inefficiencies, potentially affecting production quality and overall operational efficiency. And good training will require spending a lot of money.
- Regulatory and compliance considerations. Remote operations may require manufacturers to comply with additional regulations and standards, such as data privacy and safety requirements. Examples are the General Data Protection Regulation (GDPR), the Occupational Safety and Health Administration (OSHA), etc. Non-compliance can result in fines, penalties, and damage to the company's reputation.
- High cost of equipment and infrastructure. Remote operations require reliable and secure equipment and infrastructures like the secure network system and advanced control and monitoring systems. They are costly to implement and maintain.
- Cultural resistance. Some workers may be resistant to the adoption of remote operations. This can lead to potential cultural challenges and resistance to change. Cultural resistance can then hinder the successful implementation of remote operations and result in reduced efficiency and productivity.
- Limited visibility and control. Remote operations can lead to reduced visibility and control over remote manufacturing processes. This can make it challenging to monitor compliance with manufacturing and production standards, ensure employee safety, and control product quality.
The Future of Remote Operations in Manufacturing
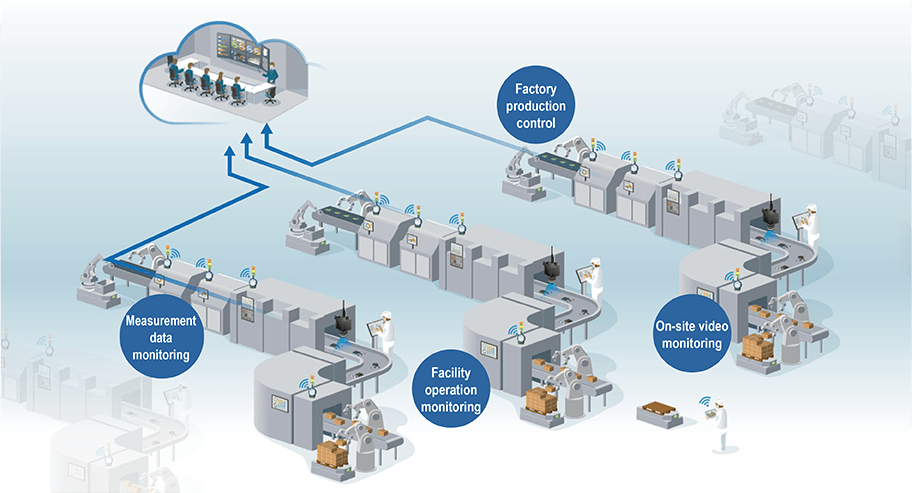
The future of remote factory operations promises a transformative shift in the manufacturing landscape. Notably, maintenance technicians and plant managers are expected to increasingly adopt remote work models increasingly, leveraging advanced technologies such as the Internet of Things (IoT) to monitor, analyze, and optimize manufacturing processes from a distance.
According to research by CB Insights, many factory owners are poised to invest significantly in IoT systems, driving the industry towards increased connectivity and automation. This adoption is anticipated to enhance real-time monitoring capabilities, facilitate predictive maintenance, and streamline overall operational efficiency.
As the manufacturing sector continues to embrace the benefits of remote operations, the workforce is likely to become more geographically dispersed, fostering a flexible and adaptive industry ecosystem. The future holds a vision where remote factory operations, empowered by IoT systems and advanced technologies, become necessary for business continuity and a cornerstone for achieving heightened productivity, efficiency, and resilience in modern manufacturing.
Recommended Literature
- Raj, R., Kumar, V., Sharma, N. K., Singh, S., Mahlawat, S., & Verma, P. (2023, April 29). The study of remote working outcome and its influence on firm performance. Social Sciences & Humanities Open. https://www.sciencedirect.com/science/article/pii/S259029112300133X
- Heredia, R. (2022, November 14). What are IoT sensors? types, uses, and examples. Zipit. https://www.zipitwireless.com/blog/what-are-iot-sensors-types-uses-and-examples
- Kolski, C., & Millot, P. (n.d.). HUMAN PROBLEMATICS OF TELEMAINTENANCE AND DECISION AID CRITERIA FOR TELEMAINTENANCE SYSTEM DESIGN. Research Gate. https://www.researchgate.net/figure/Collaboration-by-telephone-between-the-telemaintenance-expert-and-an-operator_fig2_254440417
- What are collaborative robots, Cobots: A3 Robotics Collaborative Robots. Automate. (n.d.). https://www.automate.org/a3-content/what-are-collaborative-robots
- What is predictive maintenance?. IBM. (n.d.). https://www.ibm.com/topics/predictive-maintenance#
- CB Insights. (2020, June 29). Research briefing: Industrial IoT & FACTORIES OF THE FUTURE. CB Insights Research. https://www.cbinsights.com/research/briefing/factory-of-the-future-manufacturing/
Subscribe to our newsletters
Stay ahead of the curve. Subscribe to our newsletter and receive exclusive insights, future trends, and expert knowledge delivered straight to your inbox.